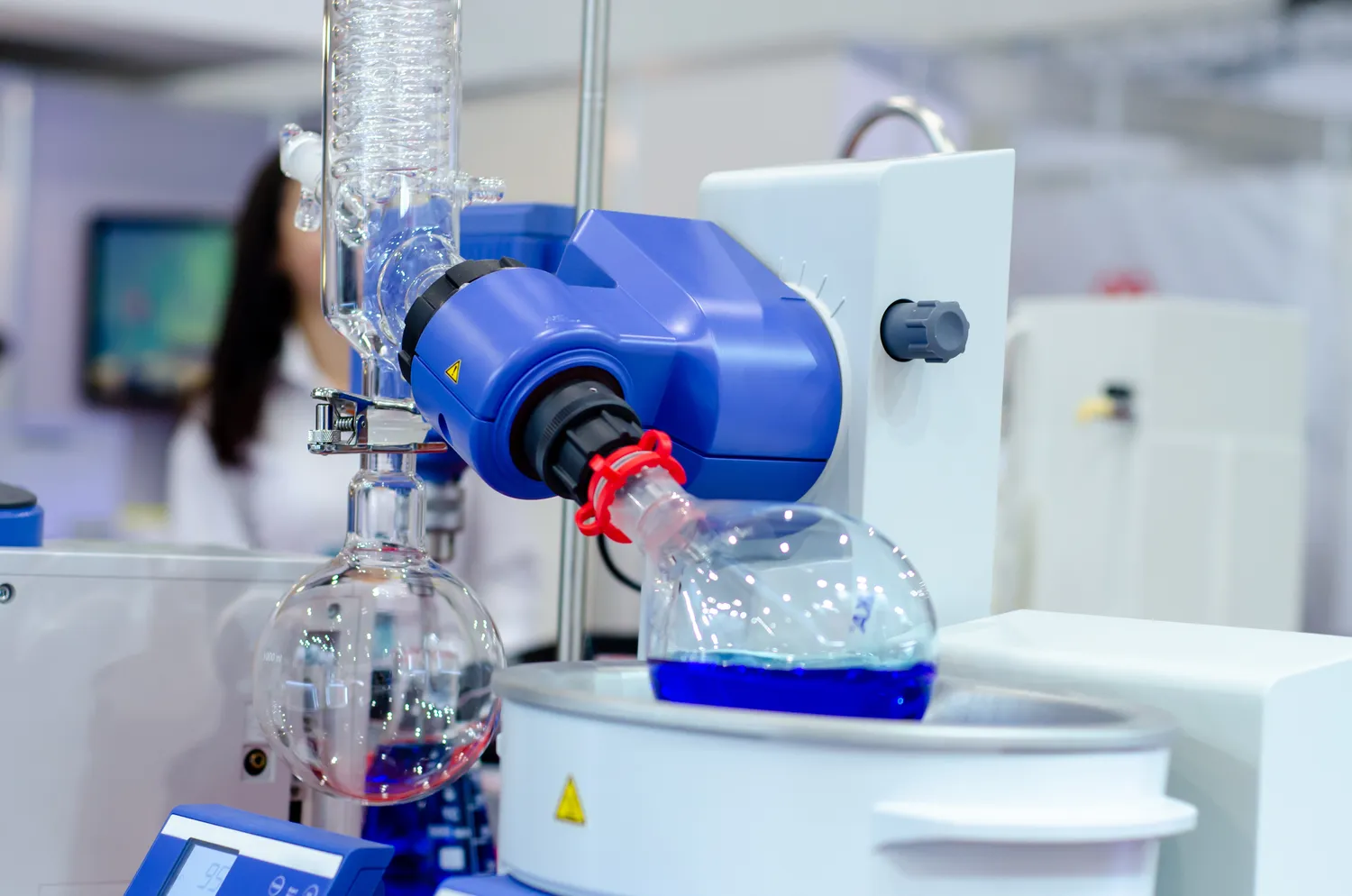
Przemysł 4.0 co to?
Przemysł 4.0 to termin, który odnosi się do czwartej rewolucji przemysłowej, charakteryzującej się integracją nowoczesnych technologii w procesach produkcyjnych. W przeciwieństwie do wcześniejszych rewolucji, które koncentrowały się głównie na mechanizacji i automatyzacji, Przemysł 4.0 wprowadza elementy cyfryzacji oraz inteligentnych systemów, które umożliwiają bardziej efektywne zarządzanie produkcją. Kluczowymi technologiami związanymi z tym zjawiskiem są Internet rzeczy, sztuczna inteligencja, big data oraz robotyka. Dzięki tym innowacjom przedsiębiorstwa mogą zbierać i analizować ogromne ilości danych w czasie rzeczywistym, co pozwala na optymalizację procesów oraz szybsze podejmowanie decyzji. Warto zauważyć, że Przemysł 4.0 nie tylko wpływa na samą produkcję, ale także na cały łańcuch dostaw oraz relacje z klientami.
Jakie technologie są kluczowe w Przemysłu 4.0
W kontekście Przemysłu 4.0 istnieje wiele technologii, które odgrywają istotną rolę w transformacji procesów produkcyjnych. Internet rzeczy (IoT) to jedna z najważniejszych innowacji, która pozwala na połączenie maszyn i urządzeń w sieci, umożliwiając im komunikację oraz wymianę danych. Dzięki IoT można monitorować stan maszyn w czasie rzeczywistym, co pozwala na przewidywanie awarii i minimalizowanie przestojów. Kolejną kluczową technologią jest sztuczna inteligencja (AI), która umożliwia analizę danych oraz automatyzację procesów decyzyjnych. AI może wspierać pracowników w podejmowaniu lepszych decyzji poprzez dostarczanie im odpowiednich informacji w odpowiednim czasie. Big data to kolejny istotny element Przemysłu 4.0, który pozwala na gromadzenie i analizowanie ogromnych zbiorów danych pochodzących z różnych źródeł. Dzięki temu przedsiębiorstwa mogą lepiej rozumieć potrzeby swoich klientów oraz optymalizować swoje działania.
Jakie korzyści przynosi wdrożenie Przemysłu 4.0
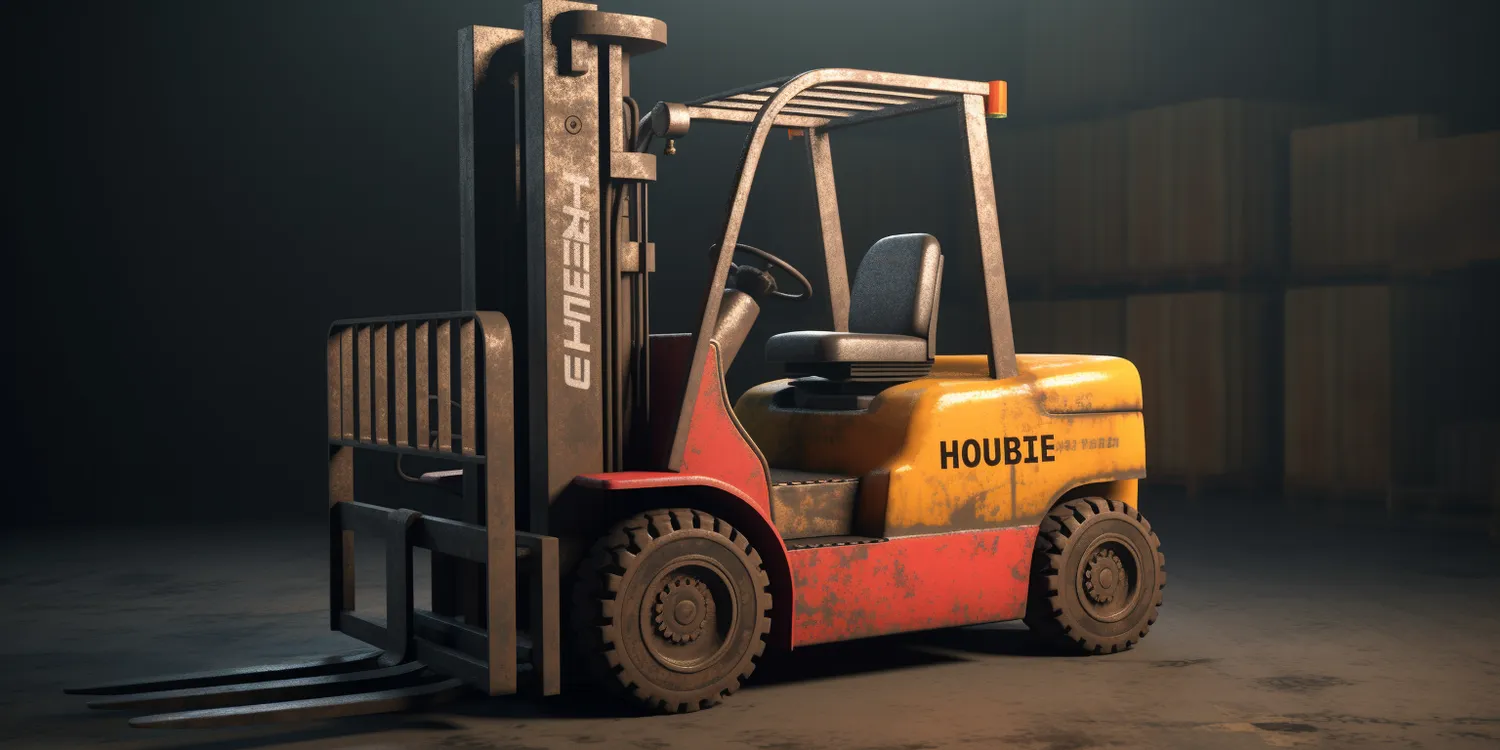
Wdrożenie rozwiązań związanych z Przemysłem 4.0 niesie ze sobą szereg korzyści dla przedsiębiorstw oraz ich pracowników. Po pierwsze, dzięki automatyzacji procesów produkcyjnych możliwe jest zwiększenie wydajności oraz redukcja kosztów operacyjnych. Maszyny i systemy oparte na sztucznej inteligencji mogą pracować przez całą dobę bez przerw, co znacząco przyspiesza produkcję i pozwala na realizację większej liczby zamówień w krótszym czasie. Po drugie, dzięki lepszemu zarządzaniu danymi przedsiębiorstwa mogą podejmować bardziej świadome decyzje oparte na rzetelnych informacjach analitycznych, co prowadzi do poprawy jakości produktów oraz usług. Kolejną korzyścią jest możliwość personalizacji oferty dla klientów, co staje się coraz ważniejsze w erze indywidualizacji rynku. Klienci oczekują produktów dostosowanych do ich potrzeb i preferencji, a technologie Przemysłu 4.0 umożliwiają szybkie dostosowanie produkcji do tych oczekiwań.
Jakie wyzwania wiążą się z Przemysłem 4.0
Mimo licznych korzyści płynących z wdrożenia Przemysłu 4.0 istnieją również istotne wyzwania, które przedsiębiorstwa muszą pokonać podczas transformacji cyfrowej. Jednym z największych problemów jest konieczność inwestycji w nowoczesne technologie oraz infrastrukturę IT, co może być kosztowne dla wielu firm, zwłaszcza małych i średnich przedsiębiorstw. Dodatkowo wiele organizacji boryka się z brakiem odpowiednich umiejętności wśród pracowników, co utrudnia skuteczne wdrażanie nowych rozwiązań technologicznych. W związku z tym konieczne staje się inwestowanie w szkolenia oraz rozwój kompetencji zespołów pracowniczych, aby mogli oni efektywnie korzystać z nowoczesnych narzędzi i systemów. Kolejnym wyzwaniem jest zapewnienie bezpieczeństwa danych oraz ochrony przed cyberatakami, które stają się coraz bardziej powszechne w erze cyfrowej transformacji.
Jak Przemysł 4.0 wpływa na rynek pracy i zatrudnienie
Przemysł 4.0 ma znaczący wpływ na rynek pracy, co budzi zarówno obawy, jak i nadzieje wśród pracowników oraz pracodawców. Z jednej strony automatyzacja i wprowadzenie robotów do procesów produkcyjnych mogą prowadzić do redukcji miejsc pracy w niektórych sektorach, zwłaszcza tych, które opierają się na rutynowych zadaniach. Wiele tradycyjnych ról może zostać zastąpionych przez maszyny, co rodzi pytania o przyszłość zatrudnienia w branżach takich jak produkcja czy logistyka. Z drugiej strony Przemysł 4.0 stwarza nowe możliwości zatrudnienia w obszarach związanych z technologią, inżynierią oraz zarządzaniem danymi. W miarę jak firmy adaptują się do nowych rozwiązań, rośnie zapotrzebowanie na specjalistów z zakresu analizy danych, programowania oraz zarządzania systemami informatycznymi. W rezultacie konieczne staje się przekształcenie edukacji zawodowej oraz programów szkoleniowych, aby przygotować przyszłych pracowników do wyzwań związanych z nowoczesnym rynkiem pracy.
Jakie są przykłady wdrożeń Przemysłu 4.0 na świecie
W ostatnich latach wiele firm na całym świecie zdecydowało się na wdrożenie rozwiązań związanych z Przemysłem 4.0, co przyniosło im wymierne korzyści. Jednym z najbardziej znanych przykładów jest niemiecka firma Siemens, która zainwestowała w inteligentne fabryki, gdzie zastosowano zaawansowane technologie takie jak IoT i sztuczna inteligencja do optymalizacji procesów produkcyjnych. Dzięki tym rozwiązaniom Siemens osiągnął znaczną poprawę wydajności oraz jakości swoich produktów. Inny przykład to amerykański producent samochodów Ford, który wprowadził roboty współpracujące w swoich liniach produkcyjnych, co pozwoliło na zwiększenie elastyczności produkcji oraz skrócenie czasu realizacji zamówień. W Azji wiele firm również dostrzega potencjał Przemysłu 4.0; japoński koncern Toyota wdraża rozwiązania oparte na big data i analizie danych w celu optymalizacji swojego łańcucha dostaw.
Jakie są kluczowe trendy w rozwoju Przemysłu 4.0
Rozwój Przemysłu 4.0 wiąże się z wieloma kluczowymi trendami, które kształtują przyszłość produkcji oraz zarządzania przedsiębiorstwami. Jednym z najważniejszych trendów jest wzrost znaczenia cyfrowych bliźniaków, czyli wirtualnych modeli rzeczywistych obiektów lub procesów, które pozwalają na symulację i optymalizację działań przed ich wdrożeniem w rzeczywistości. Dzięki temu firmy mogą testować różne scenariusze oraz podejmować lepsze decyzje dotyczące produkcji i zarządzania zasobami. Kolejnym istotnym trendem jest rozwój technologii blockchain, która umożliwia bezpieczne przechowywanie danych oraz śledzenie produktów w całym łańcuchu dostaw. Blockchain może przyczynić się do zwiększenia transparentności oraz bezpieczeństwa transakcji handlowych, co jest szczególnie ważne w kontekście rosnącej liczby cyberataków. Również rozwój sztucznej inteligencji i uczenia maszynowego staje się kluczowym elementem Przemysłu 4.0; te technologie pozwalają na automatyzację procesów analizy danych oraz wspierają podejmowanie decyzji opartych na danych historycznych i prognozach rynkowych.
Jakie są przyszłe kierunki rozwoju Przemysłu 4.0
Patrząc w przyszłość, można zauważyć kilka kluczowych kierunków rozwoju Przemysłu 4.0, które będą miały istotny wpływ na sposób funkcjonowania przedsiębiorstw oraz ich interakcje z otoczeniem rynkowym. Po pierwsze, dalsza integracja technologii cyfrowych z procesami produkcyjnymi stanie się normą; przedsiębiorstwa będą dążyć do pełnej automatyzacji swoich zakładów poprzez zastosowanie zaawansowanych systemów zarządzania produkcją opartych na sztucznej inteligencji oraz IoT. Po drugie, rozwój technologii chmurowych umożliwi firmom łatwiejszy dostęp do danych oraz narzędzi analitycznych, co przyczyni się do większej elastyczności i szybkości działania w odpowiedzi na zmieniające się potrzeby rynku. Kolejnym kierunkiem będzie wzrost znaczenia współpracy między przedsiębiorstwami a start-upami technologicznymi; wiele dużych firm zaczyna dostrzegać wartość innowacji generowanych przez młodsze firmy i decyduje się na partnerstwa strategiczne w celu szybszego wdrażania nowoczesnych rozwiązań technologicznych.
Jakie są różnice między Przemysłem 4.0 a wcześniejszymi rewolucjami przemysłowymi
Aby lepiej zrozumieć znaczenie Przemysłu 4.0, warto przyjrzeć się różnicom między tą rewolucją a wcześniejszymi etapami rozwoju przemysłowego. Pierwsza rewolucja przemysłowa miała miejsce pod koniec XVIII wieku i była związana z mechanizacją produkcji dzięki wynalezieniu maszyn parowych oraz mechanicznych urządzeń tkackich; skoncentrowała się głównie na zwiększeniu wydajności pracy fizycznej ludzi poprzez zastępowanie ich maszynami. Druga rewolucja przemysłowa nastąpiła na początku XX wieku i charakteryzowała się masową produkcją oraz zastosowaniem elektryczności; to wtedy pojawiły się taśmy montażowe i standardyzacja produktów, co znacznie obniżyło koszty produkcji i zwiększyło dostępność towarów dla konsumentów. Trzecia rewolucja przemysłowa miała miejsce od lat 70-tych XX wieku i była związana z automatyzacją procesów dzięki komputerom oraz technologiom informacyjnym; to wtedy zaczęto wykorzystywać komputery do sterowania maszynami i monitorowania procesów produkcyjnych w czasie rzeczywistym.
Polecamy zobaczyć:
-
Przemysł 4.0 - co to?
Przemysł 4.0 to termin, który odnosi się do czwartej rewolucji przemysłowej, charakteryzującej się integracją nowoczesnych…
-
Przemysł 4.0 co to jest?
Przemysł 4.0 to termin, który odnosi się do czwartej rewolucji przemysłowej, charakteryzującej się szerokim zastosowaniem…
-
Co to psychiatra?
Psychiatra to lekarz specjalizujący się w diagnozowaniu oraz leczeniu zaburzeń psychicznych. Jego rola w systemie…
-
Podologia co to?
Podologia to dziedzina medycyny, która zajmuje się diagnostyką oraz leczeniem schorzeń stóp i dolnych kończyn.…
-
Co to SEO?
SEO, czyli optymalizacja pod kątem wyszukiwarek internetowych, to zbiór praktyk mających na celu poprawę widoczności…
Related Posts
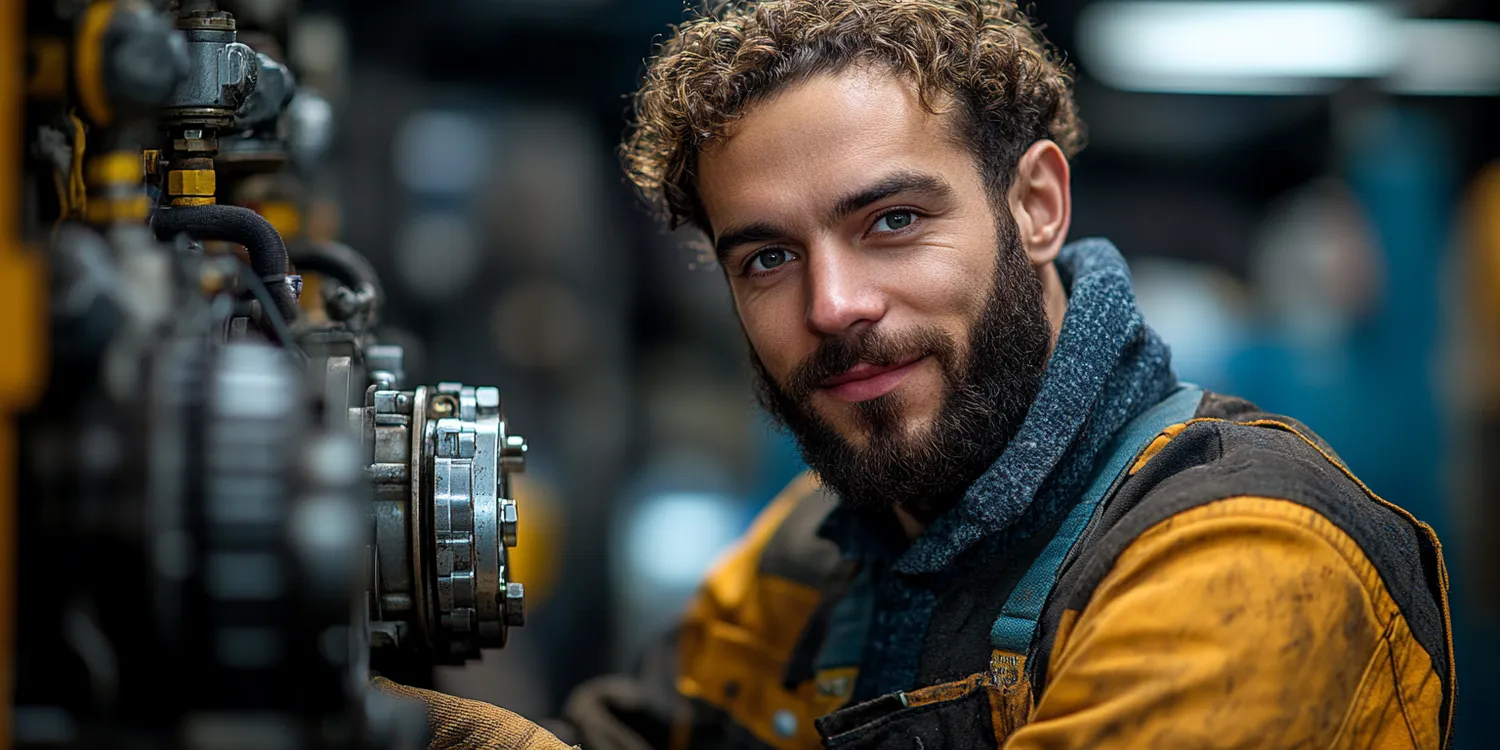
Co po studiach mechanika i budowa maszyn?
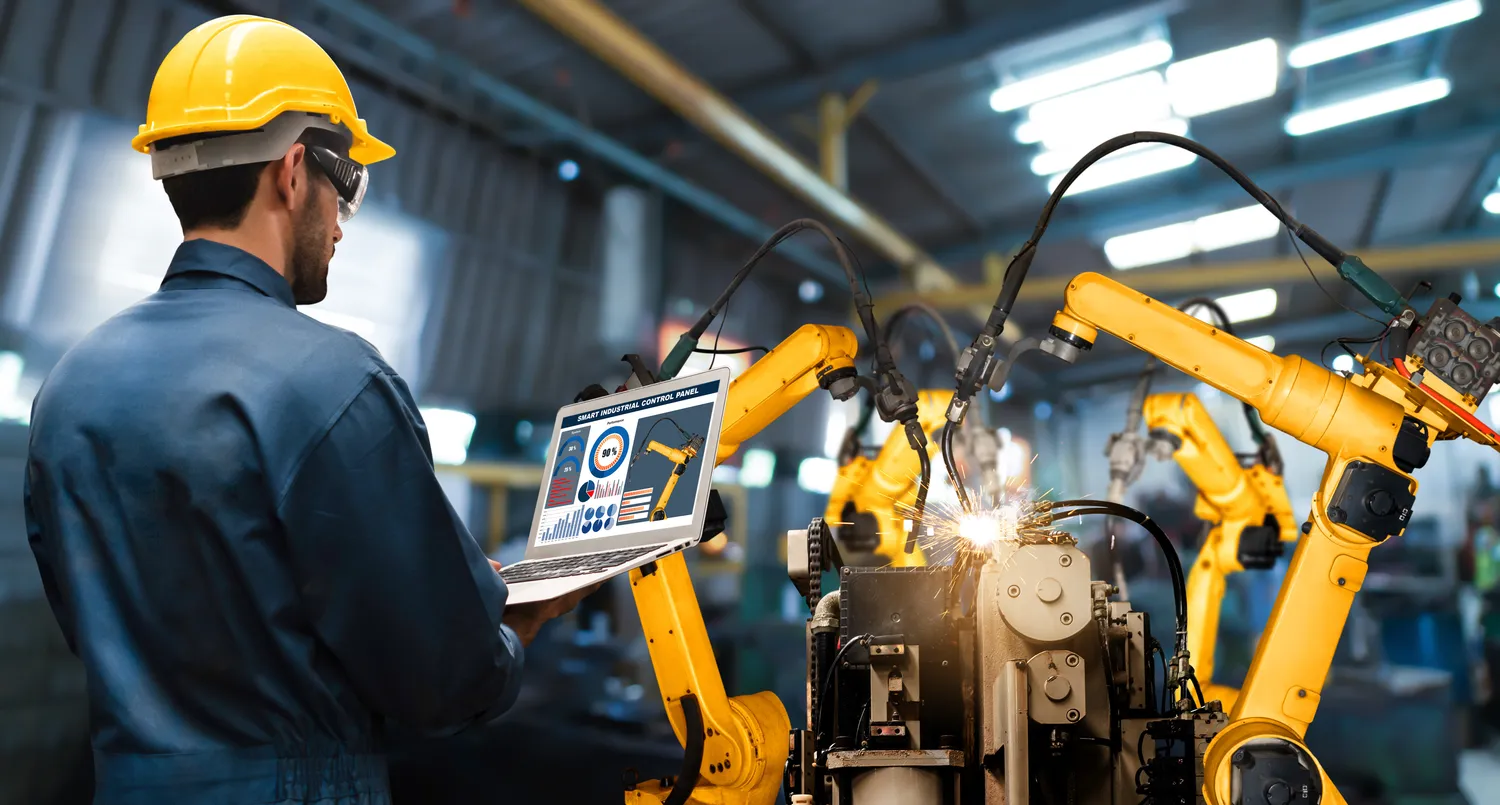
Jaki przemysł rozwijał się na ziemiach utraconych?
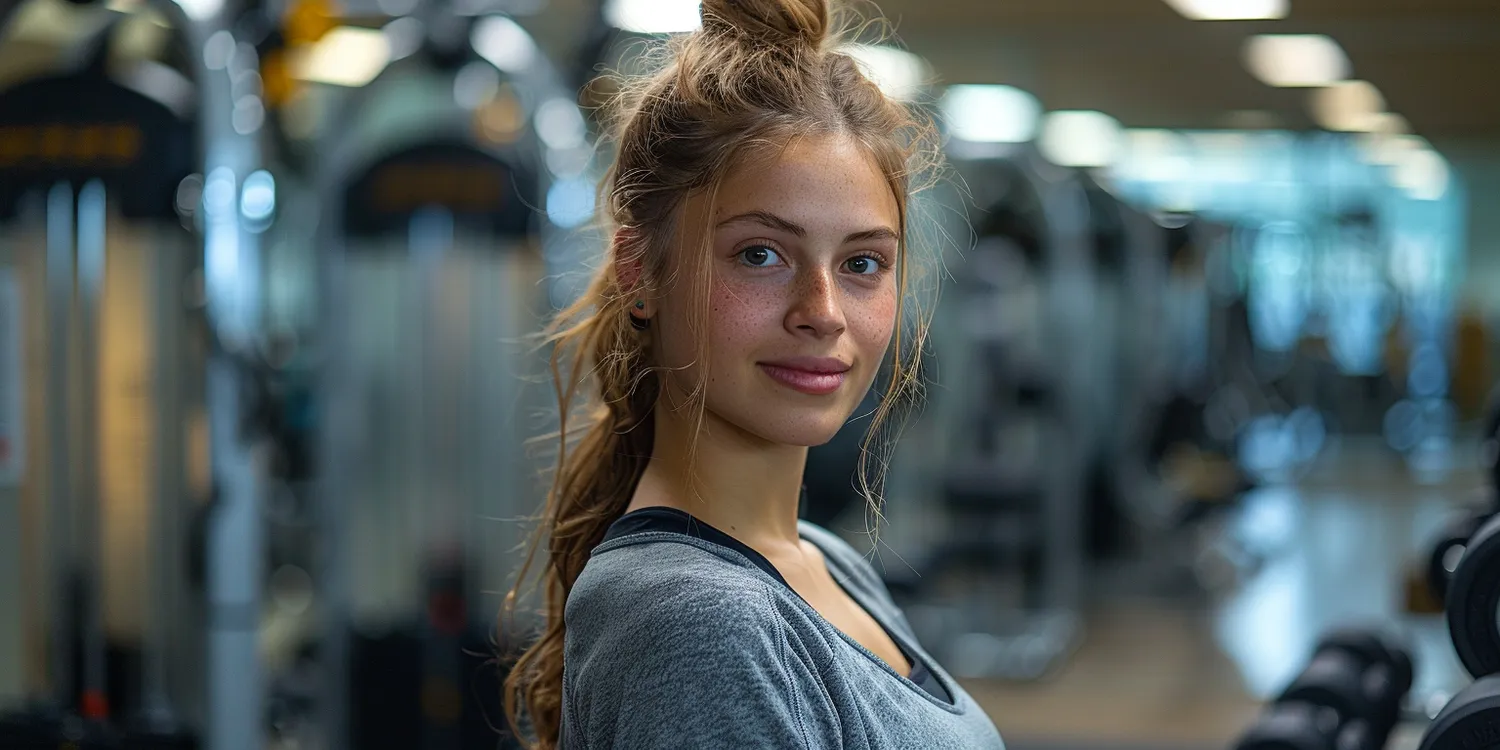