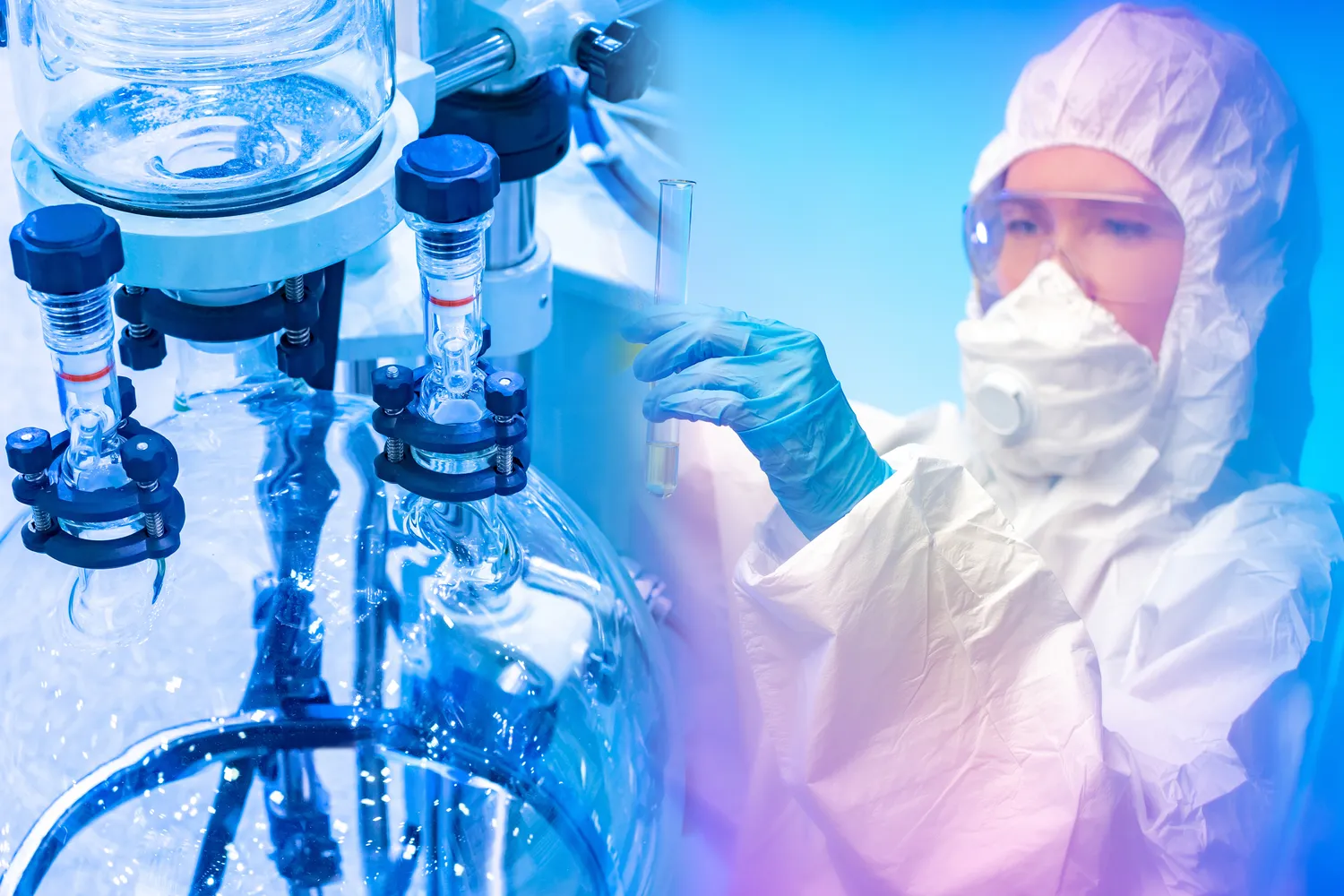
Destylator przemysłowy
Destylator przemysłowy to urządzenie, które służy do separacji cieczy na podstawie różnicy w temperaturze wrzenia. Proces ten jest kluczowy w wielu gałęziach przemysłu, takich jak chemiczny, petrochemiczny czy spożywczy. Destylacja polega na podgrzewaniu cieczy, co powoduje jej parowanie, a następnie skraplaniu pary w celu uzyskania czystego produktu. W destylatorach przemysłowych wykorzystuje się różne technologie, takie jak destylacja frakcyjna, która pozwala na oddzielenie kilku składników o różnych temperaturach wrzenia. W praktyce oznacza to, że można uzyskać z surowca wiele różnych produktów, co zwiększa efektywność procesu produkcji. Destylatory przemysłowe są zazwyczaj dużymi i skomplikowanymi urządzeniami, które wymagają precyzyjnego zarządzania temperaturą oraz ciśnieniem. Dzięki nowoczesnym technologiom możliwe jest automatyzowanie tych procesów, co zwiększa ich wydajność oraz bezpieczeństwo.
Jakie są rodzaje destylatorów przemysłowych dostępnych na rynku
Na rynku dostępnych jest wiele rodzajów destylatorów przemysłowych, które różnią się zarówno konstrukcją, jak i zastosowaniem. Najpopularniejsze z nich to destylatory prostokątne oraz kolumnowe. Destylatory prostokątne są stosunkowo proste w budowie i często wykorzystywane w mniejszych zakładach produkcyjnych. Z kolei destylatory kolumnowe charakteryzują się bardziej skomplikowaną konstrukcją i są idealne do dużych instalacji przemysłowych, gdzie potrzebna jest wysoka wydajność. Innym rodzajem są destylatory próżniowe, które działają w obniżonym ciśnieniu, co pozwala na destylację substancji o wysokiej temperaturze wrzenia bez ich rozkładu. Warto również wspomnieć o destylatorach azeotropowych, które są wykorzystywane do separacji mieszanin azeotropowych, czyli takich, które mają stały skład podczas destylacji.
Jakie zastosowania mają destylatory przemysłowe w różnych branżach
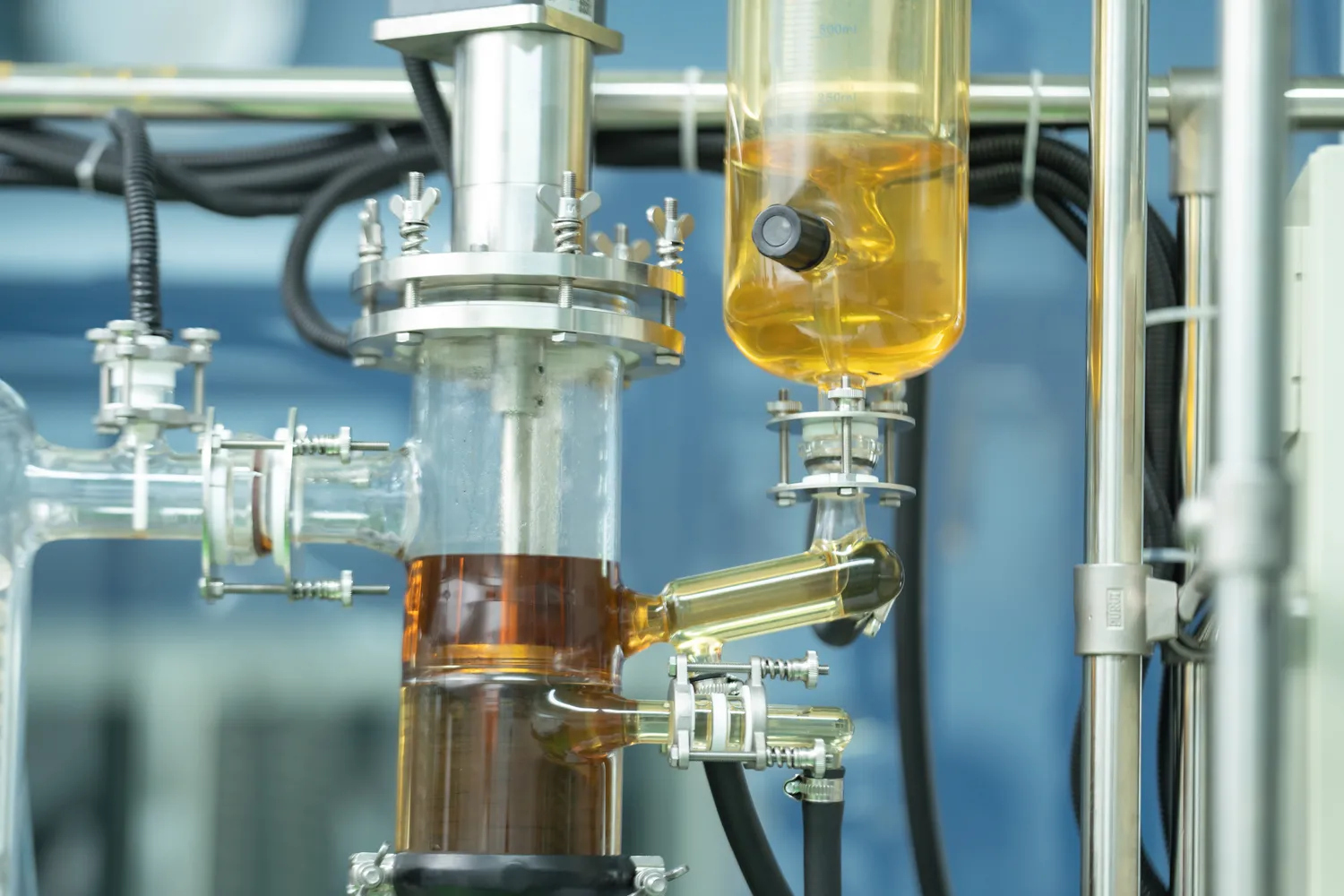
Destylatory przemysłowe znajdują szerokie zastosowanie w różnych branżach, od chemii po przemysł spożywczy. W przemyśle chemicznym są one wykorzystywane do produkcji rozpuszczalników oraz innych substancji chemicznych poprzez separację ich składników. W branży petrochemicznej destylatory odgrywają kluczową rolę w procesie rafinacji ropy naftowej, gdzie oddzielają różne frakcje paliwowe. W przemyśle spożywczym destylatory są używane do produkcji alkoholu oraz ekstraktów smakowych z roślin. Przykładem może być produkcja whiskey czy wódki, gdzie proces destylacji ma kluczowe znaczenie dla jakości finalnego produktu. Ponadto destylatory znajdują zastosowanie w farmaceutyce do oczyszczania substancji czynnych oraz w biotechnologii do separacji metabolitów.
Jakie są zalety korzystania z nowoczesnych destylatorów przemysłowych
Korzystanie z nowoczesnych destylatorów przemysłowych przynosi wiele korzyści dla przedsiębiorstw zajmujących się produkcją chemikaliów czy alkoholu. Przede wszystkim nowoczesne urządzenia charakteryzują się wyższą efektywnością energetyczną, co przekłada się na niższe koszty operacyjne. Dzięki zaawansowanym systemom automatyzacji możliwe jest precyzyjne kontrolowanie wszystkich parametrów procesu destylacji, co zwiększa jakość finalnych produktów. Nowoczesne destylatory często wyposażone są w technologie umożliwiające ciągłą pracę, co pozwala na zwiększenie wydajności produkcji oraz minimalizację przestojów związanych z konserwacją czy naprawami. Dodatkowo wiele nowych modeli posiada funkcje monitorowania i analizy danych w czasie rzeczywistym, co ułatwia zarządzanie procesem produkcji oraz identyfikację potencjalnych problemów zanim staną się one poważne. Warto także zauważyć, że nowoczesne rozwiązania często uwzględniają aspekty ekologiczne poprzez zmniejszenie emisji szkodliwych substancji oraz optymalizację zużycia surowców naturalnych.
Jakie są kluczowe elementy konstrukcyjne destylatorów przemysłowych
Destylatory przemysłowe składają się z kilku kluczowych elementów konstrukcyjnych, które są niezbędne do prawidłowego funkcjonowania całego urządzenia. Podstawowym elementem jest zbiornik, w którym następuje podgrzewanie cieczy. Zbiornik ten musi być wykonany z materiałów odpornych na wysoką temperaturę oraz korozję, aby zapewnić długotrwałe użytkowanie. Kolejnym istotnym elementem jest kolumna destylacyjna, która pełni rolę miejsca separacji składników. W kolumnie znajdują się różne elementy, takie jak wypełnienia czy talerze, które zwiększają powierzchnię kontaktu między parą a cieczą, co pozwala na efektywniejszą separację. Ważnym komponentem jest również skraplacz, który przekształca parę z powrotem w ciecz. Skraplacze mogą mieć różne formy, w zależności od wymagań procesu i rodzaju substancji. Dodatkowo destylatory wyposażone są w systemy kontrolne, które monitorują temperaturę, ciśnienie oraz inne parametry procesu. Te elementy współpracują ze sobą, aby zapewnić optymalną wydajność i jakość destylacji.
Jakie czynniki wpływają na wydajność destylatorów przemysłowych
Wydajność destylatorów przemysłowych zależy od wielu czynników, które mogą wpływać na efektywność procesu separacji. Jednym z najważniejszych aspektów jest temperatura podgrzewania cieczy. Zbyt niska temperatura może prowadzić do niedostatecznego parowania substancji, podczas gdy zbyt wysoka może powodować rozkład niektórych składników. Kolejnym czynnikiem jest ciśnienie panujące w systemie; obniżenie ciśnienia może zwiększyć wydajność destylacji dla substancji o wysokiej temperaturze wrzenia. Warto również zwrócić uwagę na czas trwania procesu – zbyt krótki czas może skutkować niepełną separacją składników, natomiast zbyt długi może prowadzić do strat materiałowych. Jakość używanych materiałów oraz ich czystość także mają znaczenie; zanieczyszczenia mogą wpłynąć na proces oraz jakość finalnego produktu. Dodatkowo odpowiedni dobór elementów konstrukcyjnych destylatora, takich jak kolumna czy skraplacz, ma kluczowe znaczenie dla osiągnięcia optymalnej wydajności.
Jakie są najczęstsze problemy związane z destylatorami przemysłowymi
Destylatory przemysłowe, mimo swojej zaawansowanej technologii, mogą napotykać różnorodne problemy podczas eksploatacji. Jednym z najczęstszych problemów jest osadzanie się zanieczyszczeń w kolumnach destylacyjnych, co prowadzi do zmniejszenia efektywności separacji składników. Osady te mogą pochodzić z surowców lub być wynikiem reakcji chemicznych zachodzących podczas procesu. Innym problemem są wahania temperatury i ciśnienia, które mogą prowadzić do niestabilności procesu oraz obniżenia jakości produktów końcowych. Często występującym problemem są również awarie systemów kontrolnych i automatyzacji, które mogą skutkować błędami w procesie produkcji i koniecznością przestoju urządzenia. Zdarza się także, że destylatory nie osiągają zakładanej wydajności z powodu niewłaściwego doboru parametrów pracy lub konstrukcji urządzenia.
Jakie są koszty związane z zakupem i eksploatacją destylatorów przemysłowych
Koszty związane z zakupem i eksploatacją destylatorów przemysłowych mogą być znaczne i zależą od wielu czynników. Przede wszystkim cena samego urządzenia jest uzależniona od jego typu, wielkości oraz zastosowanych technologii. Destylatory prostokątne są zazwyczaj tańsze niż kolumnowe, które wymagają bardziej skomplikowanej konstrukcji i większej precyzji wykonania. Oprócz kosztu zakupu należy uwzględnić także koszty instalacji oraz uruchomienia urządzenia, które mogą być znaczące w przypadku dużych instalacji przemysłowych. Koszty eksploatacyjne obejmują zużycie energii elektrycznej potrzebnej do podgrzewania cieczy oraz koszty surowców wykorzystywanych w procesie produkcji. Dodatkowo należy brać pod uwagę koszty konserwacji i ewentualnych napraw urządzenia, które mogą być niezbędne w trakcie jego użytkowania.
Jakie innowacje technologiczne wpływają na rozwój destylatorów przemysłowych
Innowacje technologiczne mają ogromny wpływ na rozwój destylatorów przemysłowych i ich efektywność. W ostatnich latach obserwuje się rosnące zainteresowanie technologiami automatyzacji oraz cyfryzacji procesów produkcyjnych. Dzięki zastosowaniu zaawansowanych systemów monitorowania możliwe jest śledzenie parametrów pracy urządzenia w czasie rzeczywistym oraz szybkie reagowanie na wszelkie nieprawidłowości. Innowacyjne rozwiązania obejmują także wykorzystanie sztucznej inteligencji do optymalizacji procesów destylacji poprzez analizę danych historycznych oraz prognozowanie przyszłych trendów produkcyjnych. Ponadto rozwijają się technologie związane z wykorzystaniem odnawialnych źródeł energii w procesach produkcyjnych, co pozwala na zmniejszenie kosztów operacyjnych oraz ograniczenie negatywnego wpływu na środowisko naturalne. Nowoczesne materiały wykorzystywane do budowy destylatorów zapewniają lepszą odporność na korozję oraz wyższe parametry termiczne, co przekłada się na dłuższą żywotność urządzeń.
Jakie są przyszłe kierunki rozwoju technologii destylacyjnej
Przyszłość technologii destylacyjnej zapowiada się interesująco dzięki dynamicznemu rozwojowi nauki i technologii. Jednym z kluczowych kierunków rozwoju będzie dalsza automatyzacja procesów produkcyjnych, co pozwoli na zwiększenie wydajności oraz redukcję kosztów operacyjnych. W miarę postępującej cyfryzacji coraz więcej przedsiębiorstw będzie korzystać z systemów opartych na sztucznej inteligencji do analizy danych oraz optymalizacji procesów destylacyjnych. Również rozwój technologii związanych z odzyskiem energii stanie się istotnym aspektem w kontekście ochrony środowiska oraz zmniejszenia kosztów produkcji. Inwestycje w badania nad nowymi materiałami o lepszych właściwościach termicznych i chemicznych będą miały kluczowe znaczenie dla poprawy efektywności energetycznej destylatorów przemysłowych. Ponadto rosnące zainteresowanie ekologicznymi metodami produkcji sprawi, że techniki takie jak ekstrakcja cieczy czy membranowa separacja będą coraz częściej stosowane jako alternatywy dla tradycyjnej destylacji.